- Codes and Standards

The IBC’s modification to exit access travel distance
Understanding the international building code’s increase for group f-1 and s-1 occupancy..
The 2015 International Building Code includes a key modification, increasing the length of exit access travel distance from 250 ft to 400 ft (if it meets specific criteria) for buildings containing Group F-1 and/or S-1 occupancy.
This change is significant to the design industry, building owners and occupants of large distribution and manufacturing facilities. Understanding the code’s implications for your existing and future facilities will ensure you’re properly prepared. A brief timeline of exit access travel distance
- 1994: In the 1994 Uniform Building Code, the exit access travel distance in a building protected with a fire sprinkler system was typically 200 ft. The exit access travel distance could be increased to 400 ft when facilities storing or manufacturing noncombustible products were provided with smoke/heat vents in addition to the fire sprinkler system.
- 1997: In the 1997 Uniform Building Code, this section was revised to allow this increase to apply to all warehouses and factories if they were protected with a fire sprinkler system and smoke/heat vents. This exit access travel distance increase resulted in larger buildings with open, undivided areas. A typical warehouse ranged from 600 to 700 ft wide. As buildings continued to grow, 600 ft became the narrow dimension for a warehouse, with many buildings exceeding 1000 ft in length.
- 2009/2012: The 2009/2012 editions of the International Building Code were revised to eliminate the 400 ft exit travel distance for large Group S-1 warehouses and large Group F-1 manufacturing facilities equipped with smoke and heat vents. This change was made because thermally activated vents were judged not to warrant such an increase.
The effects of eliminating the 400 ft exit travel distance
Due to the 400 ft loss, designers had to modify new warehouse and manufacturing facilities’ proportions or incur the cost of providing additional exits. And while it was clear to many in the industry that the original rationale for 400 ft was faulty, eliminating the requirement in its entirety was not an option.
The industry focused on ways to increase the travel distance for large buildings containing Group F-1 and/or S-1 occupancy.
Task group 400
An industry group in California came together as "Task Group 400" and conducted a fire modeling study, which demonstrated that the vast volume of large buildings could be used to contain smoke.
The group’s report was reviewed by the California State Fire Marshal’s Office and presented to the California Building Standard Commission, requesting a reinstatement of the 400 ft travel distance without any special protection, provided all of the following are met:
1. The portion of the building classified as Group F-1 or S-1 is limited to one story in height.
2. The minimum height from the finished floor to the bottom of the ceiling or roof slab or deck is 24 ft.
3. The building is equipped throughout with an automatic fire sprinkler system in accordance with section 903.3.1.1.
The exit access travel distance reversal was successfully passed, and California adopted an amended version of the 2009 International Building Code as the 2010 California Building Code.
California’s code change was later adopted into the 2015 edition of the International Building Code – the model code for most states.It should be noted that, although code no longer requires smoke and heat vents for this travel distance increase, vents or mechanical smoke removal system, are still required by Section 910.3 and 910.4 for Group S-1 and F-1 buildings of more than 50,000 sq ft. There are exceptions, however, for frozen food warehouses and areas with specific types of sprinkler systems.
Sonja Antunovic-Curcic has over 15 years of experience in architectural design. She has a strong technical background and ability to effectively transform challenges into opportunities. Her experience involves design of new buildings, expansions or alterations to existing buildings. This article originally appeared on Stellar Food for Thoughts . Stellar is a CFE Media content partner. Edited by Joy Chang, digital project manager, CFE Media, [email protected]
Do you have experience and expertise with the topics mentioned in this content? You should consider contributing to our CFE Media editorial team and getting the recognition you and your company deserve. Click here to start this process.
- Use NFPA 3 for new, existing buildings
- Reviewing the 2014 NEC
- Fire and life safety: Six trends that matter to engineers
Related Resources
Privacy overview.
Escape travel distances
Further guidance regarding escape routes This section provides further guidance on the general principles that apply to escape routes and provides examples of typical escape route solutions for a range of common building layouts. The guidance is based on premises of normal risk so if your premises (or part of your premises) are higher (or lower) risk you should adapt the solution accordingly. Travel distances Having established the number and location of people and the exit capacity required to evacuate them safely, you now need to confirm that the number and location of existing exits is adequate. This is normally determined by the distance people have to travel to reach them. In new buildings which have been designed and constructed in accordance with modern building standards the travel distances will already have been calculated. Once you have completed your fire risk assessment you need to confirm that those distances are still relevant. When assessing travel distances you need to consider the distance to be travelled by people when escaping, allowing for walking around furniture or display material etc. The distance should be measured from all parts of the premises (e.g. from the most remote part of an office or shop on any floor) to the nearest place of reasonable safety which is: A protected stairway enclosure (a storey exit) A separate fire compartment from which there is a final exit to a place of total safety. The nearest available final exit Suggested travel distances Where more than one escape route is provided: 25m in higher fire-risk area. 45M in normal fire-risk area. 60m in lower fire-risk area. Where only a single escape route is provided: 12m in higher fire-risk area. 18m in normal fire-risk area. 25m in lower fire-risk area. The travel distances given above are based on those recommended in Approved Document B of the Building Regulation and are intended to complement the other fire safety recommendations in Approved Document B. Your current escape route travel distances may be different from these since they may be based on recommendations made in alternative guidance. Where your route leads to more than one final exit, but only allows initial travel in a single direction (e.g. from a room or dead end), then this initial travel distance should be limited to that for a "single escape route". However, your total travel distance should not exceed that for "more than one escape route". Measuring travel distance The route taken through a room or space will be determined by the layout of the contents e.g. work stations, aisle layout. It is good practice to ensure routes to the exits are kept as direct and short as possible. In small rooms there may only be one exit but in larger rooms or area there may be many exits. In some cases where the contents are moved around or the space is liable to frequent change, e.g. in a storage area or where racking is moveable you should ensure that the exits, or the routes to them, do not become blocked or the length of the route is not significantly extended.


Warehouse Putaway Process: Types, Ways To Optimize & Benefits
A guide explaining the putaway process in a warehouse, exploring different types of warehouse putaway processes, highlighting the advantages of an efficient putaway process, and outlining key strategies to optimize this critical aspect of warehouse management.
In this blog
Over the years, warehouse managers have repeatedly deemed the putaway process in warehouse as one of the biggest contributors to warehousing inefficiencies. In fact, 45% of all warehousing managers surveyed admitted to their putaway process being highly inefficient.
It is absolutely crucial for warehouses to have an efficient and accurate putaway process to not only enhance the pick/pack/ship process but also ensure the safety of products, equipment, and employees along with preventing situations of back-orders and stockouts. From the moment an order is placed to the moment it leaves, a warehouse keeps on moving. With putaway being one of the most important steps of the warehouse process, getting it right can be critical for your business.
What is Putaway Process in Warehouse?
The putaway process in a warehouse refers to the activity of moving items from the receiving area to the storage area. After goods are received at a warehouse, they must be inspected, sorted, and stored properly for later retrieval and order fulfillment.
Putaway in warehouse processes means storing products inside the warehouse and stacking them on shelves, containers, bins, pallets, and other assigned places. The putaway process starts with placing a purchase order to the vendor. After the vendor sends the products listed in the order, they need to be stored efficiently inside the warehouse to make the picking process easier and to have greater visibility over the inventory as well.
The primary objective of the warehouse putaway process is to ensure that the correct item is placed in the appropriate location, which ultimately will help speed up your picking process. This can effectively make warehouse operations more efficient, error-free, and fast . Moreover, the putaway process ensures that the cargo is stored in such a manner that reduces travel distance for warehouse employees. It also helps in getting the most out of the warehouse space.
Benefits of Optimized Warehouse Putaway Process
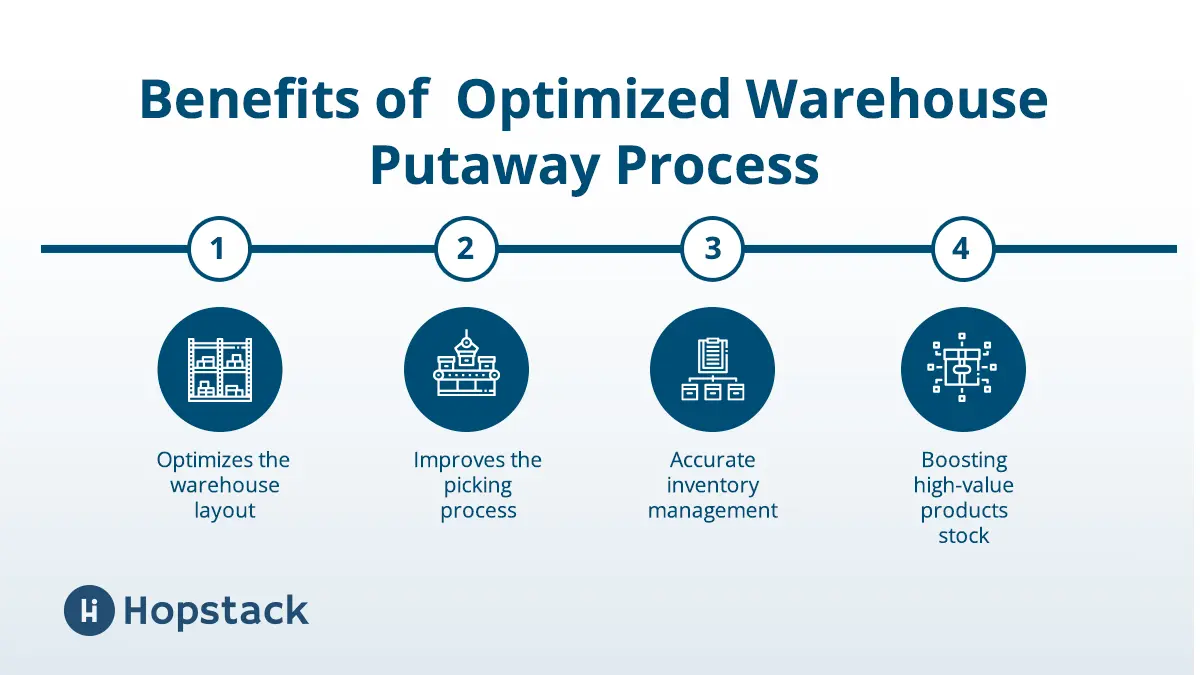
Having an efficient warehouse putaway process in place can translate into cost-saving and quicker outbound operations as explained earlier. Here are some of the key benefits a warehouse can experience by implementing a structured and effective putaway process:
Optimize the Warehouse Layout
With a carefully planned putaway process warehouse workflow , you can get the most out of your existing warehouse layout space. By combining products of the same shape and size in one location and segregating them on several different criteria, it becomes easier to store the products in their respective places. This way, you can prevent disorderly inventory management that can restrict warehouse associates from free movement and timely picking and warehouse packing .
Improve the Picking Process
Pickers spend more than half of their normal working time just wandering around the warehouse searching for the products in their order. In fact, travel can make for 50% of the total picking time and half of the overall labor cost as well. With a robust putaway process in place, they can drastically reduce the amount of time it takes to search for products and fulfill an order. An efficient automated picking process is absolutely important.
Accurate Inventory Management
Inaccurate inventory management and human-induced errors can prove costly to the business. The average picking error rate in the warehouse industry is somewhere between 1% and 3%. This relates to anywhere between $50 to $300 average cost per error with up to 13% drain on profitability. With a putaway process in place, you can keep accurate track of where each product is, what’s its quantity, and a lot more. It also reduces the chances of losing or misplacing an item.
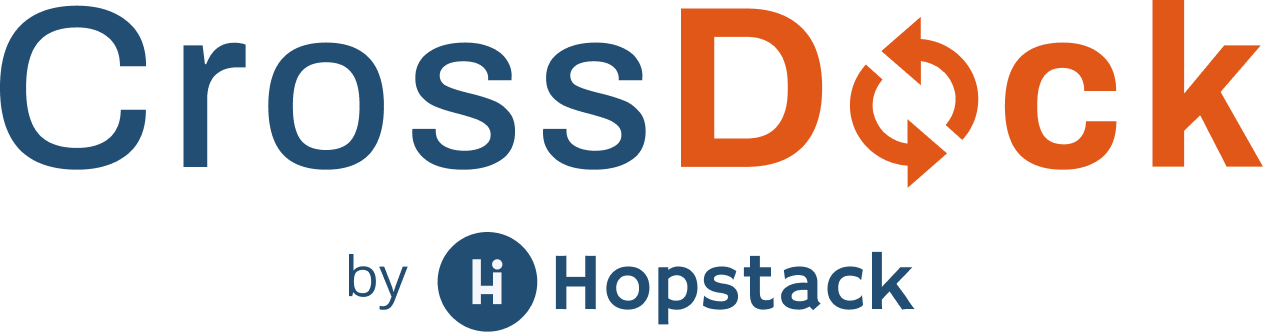
Monthly roundup of top stories in e-commerce fulfillment and warehousing.
Boost High-Value Products Stock
Keeping high-volume products at a place where they are easy to pick and keep a track of, helps in boosting the stock of that product. It also prevents pickers from searching the warehouse every time for a particular product and hence delaying the order fulfillment. If the stock is decreasing, you’ll know instantly.
Different Types of Putaway Processes in Warehouse
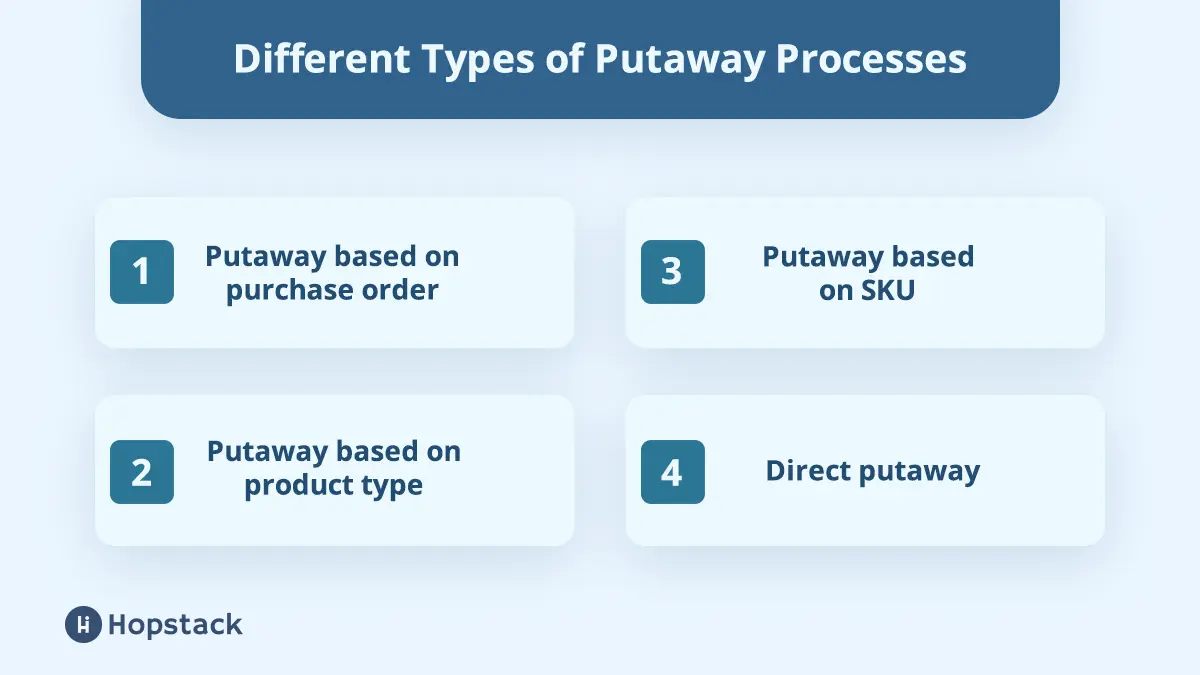
There are several different kinds of putaway processes based on the product, purchase order, SKU of the product, and more.
Putaway Based on Purchase Order
In this putaway process, similar items from different vendors are grouped together and put away in one trip. This makes it easier to pick that particular product as every stock is stored in the same place no matter where it came from. It is also helpful in weeding out any mistakes or damages as you’ll inspect every item to group them.
Putaway Based on Product Type
Putting away products based on what they are, helps in maximizing warehouse storage space utilization. This technique saves a lot of time as items of the same type can be grouped together, making it easier for pickers as they can go to where products of similar types are kept even if they don’t know where the exact product might be kept.
Putaway Based on SKU
For warehouses that store large quantities of products having the same SKU, putting them away based on their SKUs can be an efficient option. Storing products based on their manufacturer, brand, size, color, and other characteristics make them easier to find.
Direct Putaway
Direct putaway requires the least amount of handling of products. Instead of sorting through each item, in direct putaway, you can store the entire batch in a specified location. For instance, if the order is for one single customer, putting it away as it makes more sense than segregating each individual product and storing them in their designated areas.
How to Optimize the Putaway Process in a Warehouse
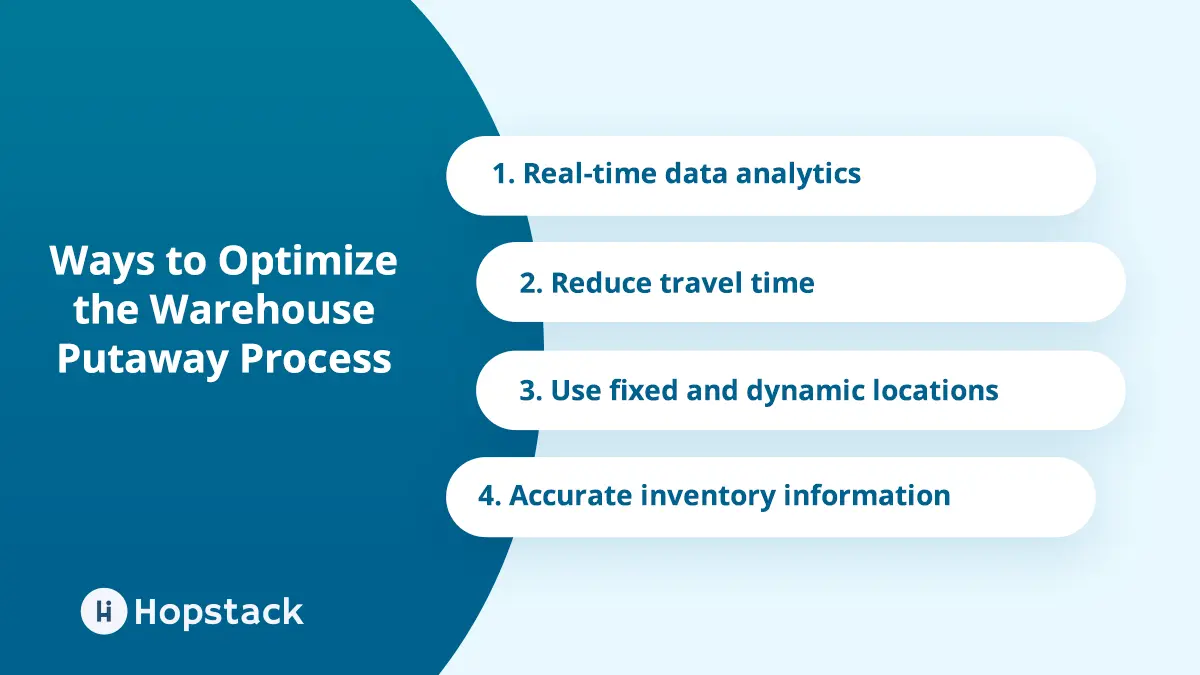
Every warehouse follows a putaway process in its own sense but without proper optimization, they won’t be able to achieve the best results. Incorporating a Warehouse Management System can help them in optimizing their warehouse putaway process and get the most out of it. Here is how WMS can optimize the putaway process for maximum operational efficiency.
Real-Time Data Analytics
Over 70% of warehouse managers have expressed their concern for not having enough data at the right time. Data about shipping frequency, cargo size, cargo type, order volume, storage availability, and more help in implementing an optimal warehouse putaway process. A WMS system can automate data collection and analyze it to suggest the best place to store a product based on different criteria.
Reduce Travel Time
The more time a picker spends searching for products, the fewer orders it can fulfill every day. In fact, estimates reveal that warehouse associates spend about 75% of their time traveling and searching for different products. With the help of an integrated WMS system, the traveling time taken to fulfill an order can be reduced. The warehouse layout can be optimized to place fast-moving products together allowing pickers to pick the items in the shortest time possible.
Use Fixed and Dynamic Locations
Using a mixture of fixed and dynamic storage can improve warehouse productivity. Employees will start remembering the location of products in fixed storage while a WMS system can help make the storage a bit versatile by placing items in the first available, temporary location. Dynamic locations could serve as a competitive advantage during peak seasons when the buying activity for certain products is high and order lead times are expected to be minimal.
Accurate Inventory Information
A WMS system provides real-time visibility on the number of stock available for a product and where it is stored. This information comes in very handy when you have to order a new batch of products and want to see the stock levels of existing products. It is also beneficial when you are receiving a new batch of products and don’t know where similar products are stored.
Implement zone putaway
Divide the warehouse into distinct zones and assign specialized teams for putaway tasks within each zone. This targeted approach enhances efficiency as teams become experts in their designated areas.
Intelligent slotting
Intelligent slotting, a fundamental warehouse management component, involves strategically placing items to optimize the putaway process. Businesses can enhance efficiency by analyzing product characteristics and demand patterns by ensuring that high-demand products are easily accessible. This proactive approach streamlines the workflow and minimizes the risk of back-orders and stockouts, improving overall customer satisfaction.
Factors Affecting the Warehouse Putaway Process
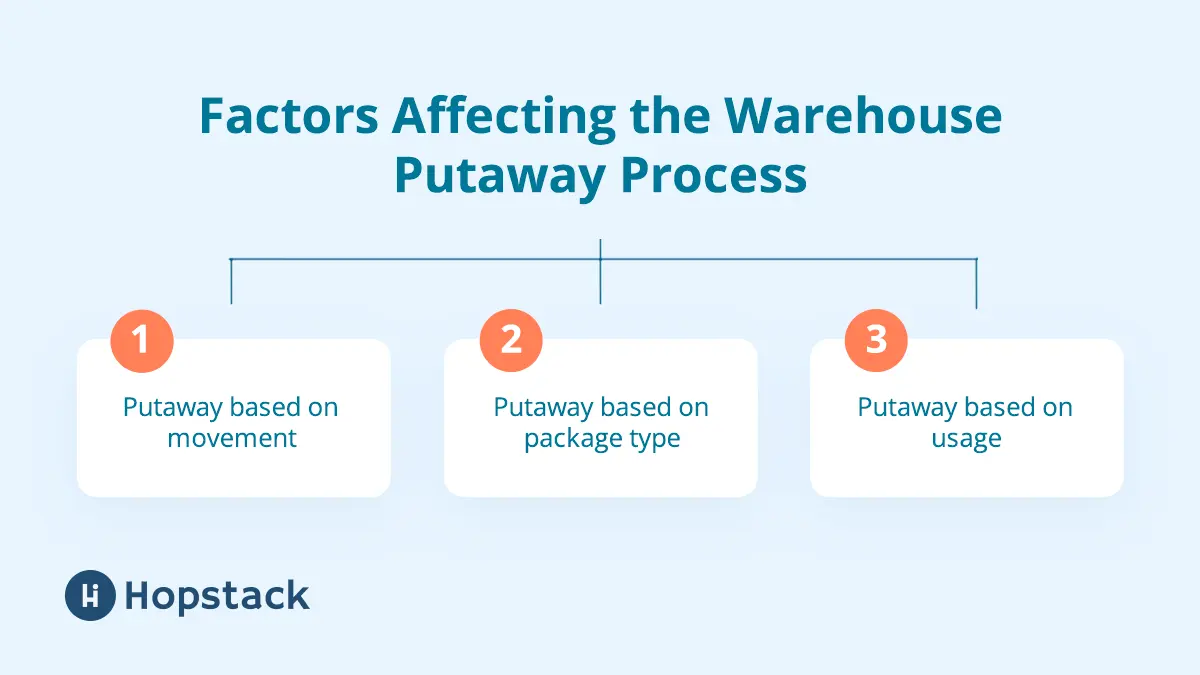
Three major factors to consider while choosing a putaway method:
Putaway Based on Movement
Using ABC analysis to store products based on their movement can reduce order fulfillment times drastically. Fast-moving products are termed as “A” category and are advised to be kept near the staging area and at a suitable height so that they can be picked and ready to ship in an instant. Similarly, slow-moving products can be termed as the “C” category and placed at the back of the warehouse.
Putaway Based on Package Type
In this method, products can be stored on their package type. For instance, individual products and pallets can be stored in different locations no matter what product they are. Similarly, packages can be distinguished based on their weight, shipment type, storage requirements, and more.
Putaway Based on Usage
There are products that are often brought together like gas stoves and utensils. Storing these products together based on their usage and why it’s being moved also helps employees in simplifying the putaway process.
Warehouse putaway KPIs and benefits
Putaway accuracy rate.
The putaway accuracy rate is a crucial KPI that measures the precision of placing items in their designated storage locations. This percentage is derived from the ratio of accurate putaways to the total number of putaways, providing insights into the effectiveness of the warehouse organization. Maintaining a high accuracy rate ensures that products are stored in the right places, minimizing picking errors and enhancing the overall accuracy of order fulfillment processes.
Putaway Cycle Time
Putaway cycle time evaluates the efficiency of the putaway process by measuring the time it takes from receiving a product to placing it in its designated storage location. This KPI helps warehouse managers identify bottlenecks and streamline operations for faster throughput. A shorter putaway cycle time improves overall warehouse efficiency and contributes to quicker product availability for customer orders.
Utilization of Storage Space
The utilization of storage space assesses how effectively the available storage space is being used. By calculating the percentage of occupied storage space relative to the total available space, this KPI aids in optimizing the layout and organization of the warehouse.
Putaway cost per Unit
Putaway cost per unit evaluates the cost efficiency of the putaway process. Calculated by dividing the total putaway costs by the number of units put away, this metric provides insights into the economic aspects of the warehouse operation. Monitoring and reducing the cost per unit can lead to cost savings and improved profitability, making the warehouse operation more financially sustainable.
Putaway Productivity
Putaway productivity measures the efficiency of the workforce during the putaway process. It is calculated by determining the number of units put away per hour or per labor hour. This KPI helps in workforce planning, resource allocation, and performance management. Improving putaway productivity contributes to overall operational efficiency, ensuring that goods are placed in storage swiftly and accurately.
Inventory Accuracy
Inventory accuracy assesses the alignment between physical inventory and recorded inventory. By calculating the percentage of accurate inventory counts, this metric ensures that the warehouse maintains reliable and precise inventory records. High inventory accuracy is essential for preventing discrepancies, avoiding stockouts, and enhancing the overall reliability of the supply chain.
Putaway Turnover
Putaway turnover reflects the frequency at which items are put away and retrieved from storage. Calculated by considering the number of items put away and retrieved relative to the total number of items in storage, this KPI provides insights into the dynamism of the warehouse operation. A higher putaway turnover indicates efficient storage practices and helps optimize inventory management strategies.
Backorder Rate
The backorder rate measures the percentage of items that cannot be put away immediately due to various constraints, such as space limitations. By calculating the ratio of back-ordered items to the total number of items to be put away, this metric provides insights into the efficiency of the putaway process and potential challenges in space management. Minimizing the backorder rate is crucial for maintaining smooth operations and ensuring the timely availability of products for customer orders.
While Picking, Packing, and Shipping are important aspects of the warehouse, the putaway process is crucial as well. However, it is still one of the most overlooked aspects of the warehouse. Companies that don’t follow an optimized warehouse putaway process can experience diminished productivity, product losses, inefficient inventory management, and more.
In today’s fast-paced and ever-changing consumption landscape, warehouses and fulfillment centers cannot afford to be complacent in their approach and let process inefficiencies hamper productivity and thus the customer experience. There is an increased need for continuous visibility and data-driven business recommendations to make all fulfillment processes error-free.
Learn more about how Hopstack’s digital warehouse platform helps in improving the putaway process by analyzing historical data on demand patterns, inventory turnover, replenishment, product characteristics, and providing recommendations for SKU location before the shipment arrives to make the process seamless.
Solving Combined Orders for North America’s Brands and Fulfillment Providers
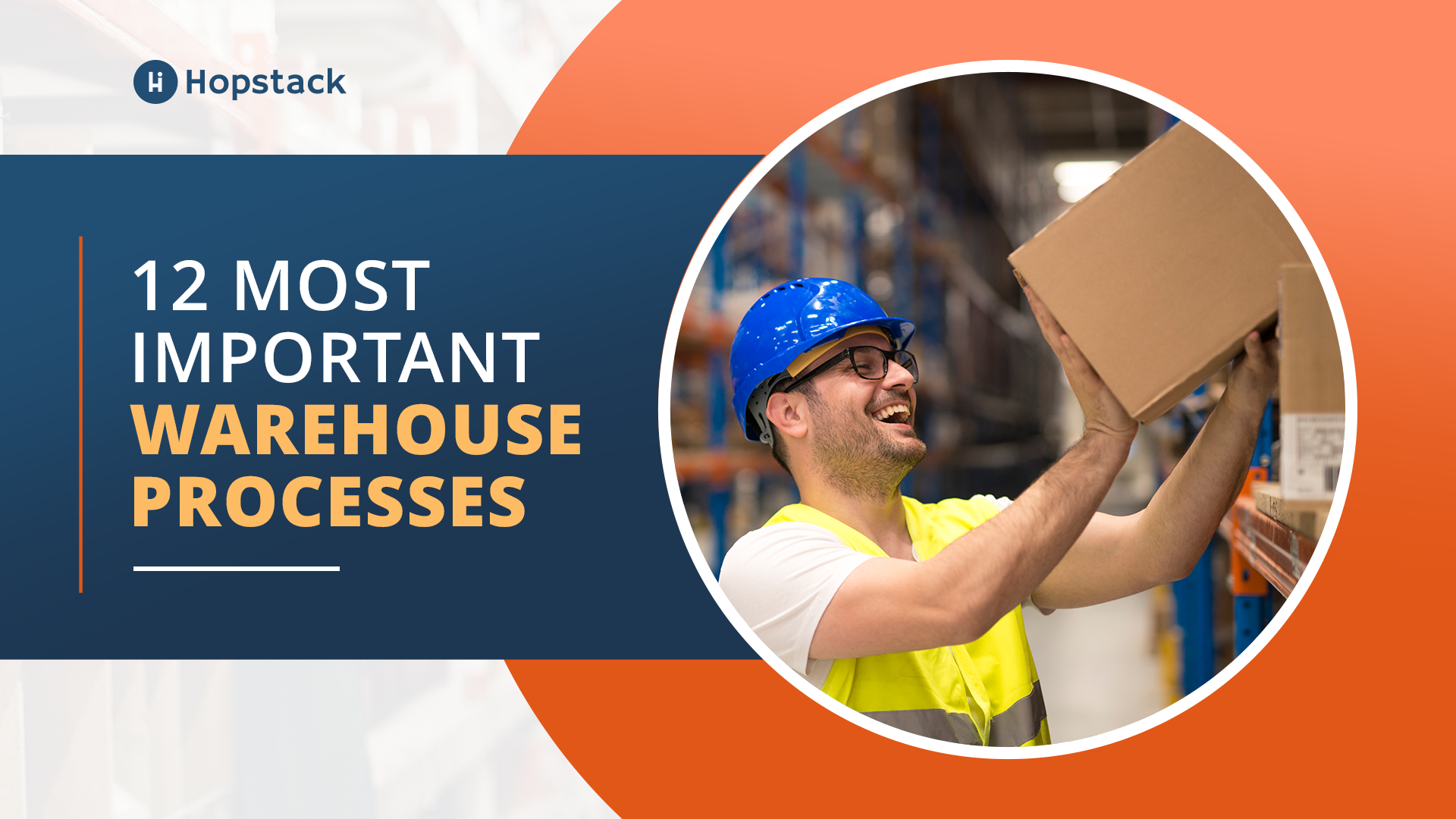
Subscribe to CrossDock, our fortnightly newsletter covering the latest in warehousing, e-commerce, and fulfillment.

How to Measure Warehouse Travel for Maximum Productivity
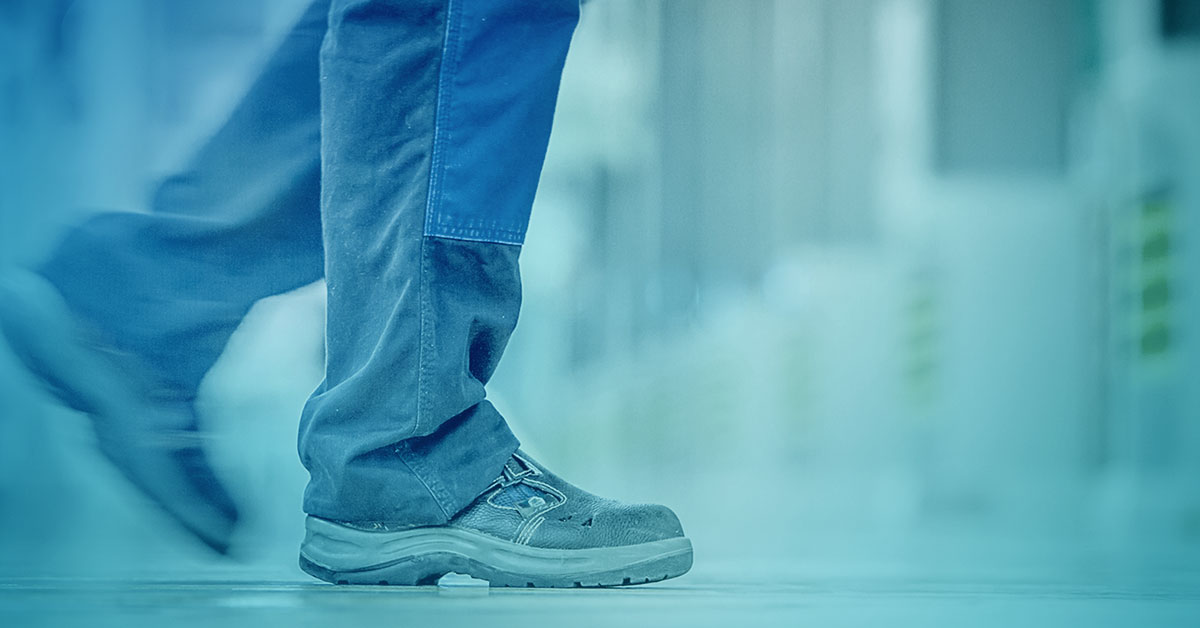
Giving proper credit for travel can be an important factor when developing labor standards for accountability or Pay-for-Performance purposes. Calculating the exact number of feet traveled by each employee may not be necessary in most situations and therefore not worth the time and cost associated with implementation and maintenance. The key is to make sure that travel is taken into consideration and that an employee gets proper credit when an above average amount of travel is required.
There are 4 main methods of measuring warehouse travel, and the best method depends upon the size of the warehouse, the type of work performed and the variability in travel between employees.
Location-Driven Method
The Location-Driven method is the simplest way to measure travel within a warehouse. It is most appropriate for smaller facilities without much variation in employee travel or operations where travel time is a small portion of the work load. An example of low variability would be where employees follow a designated pick-path or do directed put-away. Location-Driven systems usually provide “credit” for the number of orders, lines, cases and locations for each process performed by a worker. Employees are given credit for the time required to travel between locations based on an average. Sometimes they may travel a little further than the average and other times the distance may be less, but over the course of the day it will average out. While this approach is very easy to setup and maintain, it is not recommended for situations where one employee may need to travel more feet per location on average than another employee, or situations like undirected put-away where an employee may choose to place a pallet in a nearby location simply to save on the travel time.
Zone Travel Method
For many facilities, the Zone Travel method is the right balance between accuracy and simplicity. In this approach, a facility is divided into 20-150 “zones” and then the average distance between each zone is calculated. Locations are then assigned to their appropriate zones using the Location Naming Conventions. Travel can then be easily calculated as the employee moves throughout the facility based on the WMS scans. The Zone Travel Method is easy to set-up and maintain, as remapping is usually not required when new locations are added or other changes are made. “In-zone” and “Vertical” travel can also be accounted for using this method
Discrete Standards Method (x,y,z coordinates)
The Discrete Standards method is considered the industry norm for measuring warehouse travel. With Discrete Standards, each warehouse location is assigned an x, y, and z coordinate – and each movement within the warehouse is given an ideal, fully-optimized path to travel. The system then gives the employee credit based on the expected ‘ideal’ path.
There are two main challenges with this approach: 1) Discrete Standards are complicated and time-consuming to maintain. Whenever a new location is added, the warehouse must upload new coordinates. 2) When a non-ideal path is taken within the warehouse, say due to a blocked aisle, the travel calculations do not automatically adjust for the additional time that is required. While Discrete Standards are a relatively accurate approach to calculating travel, the improvement in accuracy compared to the Zone Travel method usually does not justify the additional cost and time spent on set up and maintenance.
iWarehouse Method
The newest innovation in incorporating warehouse travel into employee labor standards is Raymond’s iWarehouse system. iWarehouse improves upon traditional methods by measuring the actual distance traveled by each employee (rather than an estimate), and correcting for “exceptions” when a lift truck can’t take the optimal path. Combining the iWarehouse data with the WMS scan data gives accurate and detailed visibility into how each employee performed on each task during the day. Due to the investment required, iWarehouse is usually best fit for larger, more complex warehouses where an accurate and easy to use approach to travel is needed or for facilities where the other benefits of iWarehouse justify the investment.
Accounting for warehouse travel is an imperative component in creating fair and reasonable labor standards. There are many methods available to measure warehouse travel, and the team at Easy Metrics is happy to support our clients in determining the best method of measurement for their facilities.
Request a Custom Demo
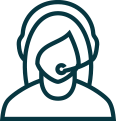
Learn how to reveal costs by employee, and to transform that data into major productivity gains
Download a Guide
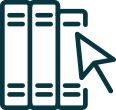
Are you finding that trying to manage your largest expense, labor, is hard, costly, and difficult? There’s a better way to get full visibility into your labor. Find out 5 ways Easy Metrics has made labor management easy.
Subscribe to the Easy Metrics Blog
Ready to make your entire team more productive.
Easy Metrics brings together all your labor data so you can understand your labor costs and drive an engaged and productive workforce.

Cookies are important to the proper functioning of a site. We take your privacy very seriously. To improve your experience, we use cookies to collect statistics to optimize site functionality, and deliver content tailored to your interests. Click Agree and Proceed to accept cookies and go directly to the site or see our privacy policy for more detail.

name; ?> --> Warehouse Operations Warehouse Operations: Optimizing the Putaway Process
The putaway process is often ignored by warehouse managers when optimizing warehouse operations but is a critical step to increasing...
By Hector Sunol • Nov 03, 2022 • 7 MIN READ
Get Warehouse Efficiency Strategies.
Stay up to date with our latest content twice a month.
Thanks for subscribing!
Please look out for an email from us! Be sure to check your spam, those filters can be tricky.
The putaway process is often ignored by warehouse managers when optimizing warehouse operations but is a critical step to increasing warehouse efficiency. The initial placement of goods has a direct impact on all subsequent warehouse processes, especially the picking process . If goods are not stored in the optimal location, travel time increases, as does the time it takes to pick and pack goods. Failing to store cargo in the optimal location also adds risk to the security/integrity of the cargo and/or the safety of the employees.
Warehouse managers suggest that inventory control (53%), picking (47%), putaway & replenishment (45%) are the most inefficient warehouse processes.
In this article, we will review some of the foremost best practices and technologies that warehouse managers can implement to optimize the putaway process and increase warehouse efficiency.
Click Here: Optimize Your Putaway Processes With This Advanced and Affordable WMS
Putaway process objective.
First, let’s review the main objective of the putaway process.
The prime objective of the putaway process is to move goods from the dock to the most optimal warehouse storage location.
At the heart of the process is assuring that:
- Cargo is stored fast and efficiently
- Warehouse travel distance is reduced to a minimum
- Security of goods and the safety of warehouse employees is ensured
- Warehouse space utilization is maximized
- Cargo is easy to find and track within the warehouse
- Goods are stored in a location that is quick and easy to retrieve during the picking process
Failing to properly implement an efficient process will have a direct impact on the productivity of warehouse operations.
Best Practices to Optimize the Putaway Process
Collect data & introduce real-time analytics.
Data is king when it comes to improving warehouse operations and implementing an efficient putaway process.
With the objective of finding the most optimal storage location, data on cargo size, weight, height, receiving and shipping frequency, cargo type (e.g. Hazmat, perishable, high value, etc.), order/sales volume, and storage availability must be consistently and accurately collected and analyzed.

Therefore, the warehouse management system (WMS) must comprise two key elements: adequate/flexible data collection capabilities and ongoing data analysis.
Once the appropriate WMS is in place, the next step is to ensure we collect data accurately and efficiently by automating collection as much as possible. This, in turn, will allow us to eliminate entry errors and reduce overhead.
For example, if we are collecting cargo weight data, an integrated digital weighing scale does the job, while a parcel or pallet dimensioning system collects data on dimensions. Both solutions automate these tasks and eliminate data entry errors.
Monitor Storage Capacity & Space Availability
Another important element in process optimization and increased warehouse efficiency is avoiding unnecessary traveling time to locations lacking space or capacity to store the cargo by monitoring storage capacity and availability.
To monitor capacity and space availability, warehouses can use barcode scanners and bin locations to track used/unused space across warehouse zones. This solution is currently available across most warehouse management systems (WMS). However, this system is prone to human error, as it relies on the warehouse clerk to scan the bin location and cargo every time he/she performs a putaway or pick task.
Another approach is to use RFIDs to automatically record tasks without any human intervention. Although this solution is still being fine-tuned and tested, RFIDs combined with more advanced solutions, such as sensors, will be part of an ecosystem of technologies that delivers real-time tracking of capacity and space within the warehouse.
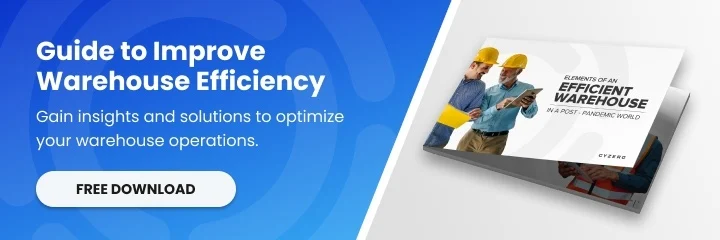
Reduce Traveling Time
Reducing traveling time is another important factor when optimizing the putaway process and warehouse operations in general. The goal is to reduce the time goods travel from the receiving area to the storage location.
Travel distance in a warehouse is 60% to 70% of labor cost.
To accomplish this, warehouse managers can conduct an ABC analysis to better understand high-volume/frequency cargo. Then, the warehouse layout should be adjusted (if necessary) to move high volume/frequency cargo closer to shipping areas, with the goal of reducing traveling time.
Note : For this to be effective, it is important to monitor order volume and frequency actively and continuously and adapt as major shifts occur.
Defining routes for the shortest path to the storage location is another way to reduce traveling time. When doing so, warehouse managers should consider factors such as distance, warehouse traffic congestion, and potential conflicts with other processes that involve traveling.
Use Direct Putaway When Possible
Another best practice is to use direct putaway when possible.
When using this method, the cargo is directly moved from its receiving area to its final location without going through a staging phase. By eliminating the need for designated staging locations, this approach not only speeds up the process but also reduces handling and space requirements in the warehouse.
When implementing this approach, it is important to remember that the WMS must be able to assign final locations from the advance shipment notice (ASN) or the point of delivery at the receiving dock. Without this capability, it is almost impossible to run an effective direct putaway process.
Use Fixed & Dynamic Locations
It’s also possible to leverage a proper mix of fixed and dynamic locations if conditions allow.
A fixed location is a pre-determined storage space, warehouse zone, aisle, or bin assigned by specific criteria. For example, a fixed location can be associated with a specific product category, customer, final destination, etc. Fixed locations help increase the efficiency of the process because warehouse clerks can memorize a cargo’s specific location assignment.
On the other hand, dynamic locations provide more flexibility by allowing clerks to put anything in the first available space they find on their way. When using dynamic locations, a reliable inventory management system to track goods and locations is paramount.
Dynamic locations can also be leveraged to temporarily store high-volume seasonal items closer to picking locations, which can be replaced with a different item(s) when volumes shift.
Keep the Warehouse Clean & Organized
Last but not least, a clean and organized warehouse/distribution center can make all the difference in running an efficient process.
A cluttered and poorly organized facility will directly impact the speed at which goods are put away. Clerks take more time to find available locations, move cargo around to open space and maneuver around obstacles to reach the desired location. Most importantly, poor warehouse organization increases safety hazards for employees and the risk of compromising the integrity of the cargo.
Without a clean and organized warehouse, streamlining your warehouse processes or using the latest warehouse technology won’t matter.
As we have learned, various ways exist to optimize the putaway process and increase warehouse efficiency. Optimizing warehouse operations through simple best practices such as keeping a clean and organized warehouse, using technology to track space utilization, or performing an ABC analysis to re-structure the warehouse layout is a matter of attention to detail, careful planning, and mindful execution.
To further increase your warehouse efficiency, check out the best practices for optimizing storage utilization .
For now, If you are ready to find the solution to optimize your warehouse, go to our Solutions Finder tool .
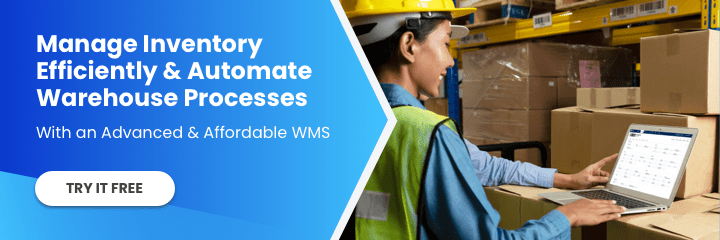
If you want more warehouse content or are curious about “Warehouse Digitalization,” you can follow us on LinkedIn , YouTube , X , or Facebook . You can also message us through our contact page if you have other inquiries. We’ll be happy to help.

Written by Hector Sunol Hector has 17 years of experience leading IT operations for large and mid-size businesses. He holds an MBA in Management and Bachelor's degree in Information Technology. Hector has a passion for books and creating opportunities for others to grow.
Related Blogs

Warehouse Operations 4 Common Warehouse Problems and How to Solve Them
Jan 13, 2023
Hector Sunol
Managing a warehouse has always been challenging. You must tackle several problems simultaneously to ensure smoo...

Warehouse Operations 5 Common Warehouse Management Mistakes You May be Making
Feb 29, 2024
Managing a warehouse isn't a piece of cake. It takes meticulous planning, execution, and monitoring to stay on t...

Business & Sales 6 Strategies to Turn Your Excess Inventory Into Revenue
Mar 05, 2024
Are you drowning in excess inventory, unsure what to do with it? If so, you're not alone. Many businesses and wa...
Blog Categories

Warehouse Operations


Information Technology

Business & Sales

Warehouse Technology

Warehouse Automation

Warehouse Management System
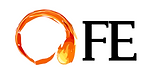
Adelaide Fire Engineers
NEWS: MARKET STUDY REVEALS GAME MECHANICS CAN DRIVE EMPLOYEE ENGAGEMENT Learn More
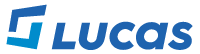
The Ultimate Guide To Reducing Warehouse Travel
In Warehouse Travel Optimization
June 30, 2021
Labor is the single largest operating cost in most DCs , and travel often accounts for half of all labor time, especially in order picking. In some DCs, pickers can travel upwards of 12 miles per shift.
To help address the warehouse travel challenge, we have put together this guide that walks through the most proven and popular warehouse travel reduction strategies distribution leaders have taken to reduce travel and improve productivity in their order picking and replenishment processes.
Table of Contents
Labor shortages and the productivity challenge, tried and true warehouse travel reduction strategies, goods-to-person picking, autonomous mobile robots, what are the advantages of amrs, a software approach to reducing warehouse travel: ai-based optimization, what are the benefits of ai-based optimization.
Labor productivity and efficiency is critical to DCs that are struggling to hire and retain workers amid tight labor markets and rising wages. Adding to the challenge, demand for warehouse workers continues to grow as companies build new fulfillment centers and expand existing facilities to satisfy the growing volume of direct-to-consumer shipments.
According to U.S. government labor statistics, the growth in eCommerce sales is driving a 10 percent annual increase in demand for warehouse labor . By 2025 ecommerce is expected to expand by an additional $1.4 trillion and account for 50% of the growth in retail. At that level, the industry will need 20 percent more DC workers than it employs today
In addition, there is an emerging shortage of hourly workers across all industries. Improving productivity is imperative for meeting the ecommerce labor challenge. And reducing warehouse travel is the lynchpin to improving productivity.
Travel in Picking and Replenishment Processes is the Lynchpin
In a conventional, non-automated picking process, travel represents the majority of the time in a DC associate’s day. Warehouse workers following an RF-picking process will typically spend more time walking or driving between pick locations than they do pulling products from bins, slots or racking locations. As illustrated by the diagram (below), hands-free voice technology can significantly reduce time at the pick face, but it does not address the travel time between picks.
For years, DCs have devoted significant efforts to reducing warehouse travel through software solutions like slotting, conventional automation, and lean process initiatives. Those efforts are taking on new urgency as ecommerce growth boosts labor demand.
Additional helpful resources
Warehouse Travel Optimization
Warehouse Optimization Tools
Warehouse Labor Management System
Advancing Warehouse Management with Voice Picking Software
3 Surefire Ways to Dramatically Reduce In-warehouse travel: Part 1-Prioritize the path and optimize picks
1) Process Engineering
The most common process-related solution to the travel challenge is to split order lines by zone (based on product velocity, type/size, etc.), and to optimize picking processes in the various pick zones. (Learn more about process optimizations in our “Ultimate Guide to Improving Warehouse Order Picking Productivity” )
Many DCs place their fastest moving piece pick items in pick modules with flow rack and conveyors. It’s not unusual for workers in a pick module using voice in a bucket brigade process to pick hundreds of lines per hour . Some Lucas customers hit 1000 picks per hour in high-density pick operations.
Slower-moving items may be batch or cluster picked so users can pick multiple orders to a cart or pallet on a single trip through a warehouse zone. Moving from single order picking to batching can dramatically reduce travel by increasing pick density (i.e., the number of picks per unit of travel).
Conventional material handling solutions often complement these process approaches to travel reduction.
2) Traditional Material Handling
Conveyors eliminate the long trips from picking areas to packing or shipping docks, and automated sortation systems improve the eciency and accuracy of assembling orders picked in multiple zones.
Automated guided vehicles (AGVs) provide an alternative to conveyors for transporting products over long distances. First introduced in the 1980s and 1990s, AGVs have evolved from track-guided systems to wire- and light-guided systems that follow set travel paths, eliminating travel from picking to staging areas.
As well will discuss later in this guide, autonomous mobile robots take this travel reduction strategy to a new level with robots that can operate anywhere in a DC.
3) Slotting
Slotting software also goes hand-in-hand with process optimization efforts by determining which products should be placed in which warehouse locations in order to improve overall warehouse efficiency. The key objective of slotting programs is to optimize product positioning, but not solely to reduce travel in picking.
Slotting solutions are based on highly engineered models of a facility that take account of product flow and picking processes, product attributes (including physical characteristics and sales volumes/velocity), and storage types, among other factors. Periodic or selective re-slotting (or slot maintenance), focuses on regularly moving products to maintain efficiency and reduce travel, among other goals.
This is similar to slot maintenance but without the consulting and engineering costs of traditional slotting solutions. (For an introduction to Machine Learning technology, read the recent Lucas white paper: Making Sense of AI and Machine Learning for the DC )
Goods-to-person picking solutions are an increasingly popular approach to reducing travel over the past 20 years. Instead of sending workers out into the DC to fetch products, good-to-person systems eliminate travel from a picking process by bringing the products to people at fixed picking stations. These solutions have evolved from carousels and AS/RS systems to highly automated “robotic” warehouses that are being built throughout the world, largely to support grocery ecommerce.
1) Carousels
Carousels have been used since the 1990s to store smaller products densely in bins on shelves that rotate to present hundreds of SKUs to a picker at a single pick or pack location. Workers may need to walk between carousel locations, but travel distances are relatively small considering the number of pick locations they can access at one position. The focus is on maximizing pick density
2) AS/RS Systems
AS/RS systems (automated storage and retrieval systems) follow a similar approach to carousels, but they often rely on rack storage and conveyor systems to transport products to workers at order assembly stations. Goods-to-person AS/RS systems eliminate travel in picking and putting products away, but high capital costs have made them unsuitable for most warehouses.
3) “Robotic” Picking Systems
Over the past 10-15 years, AS/RS systems based on shuttle technologies and dense product storage have evolved into tightly integrated “robotic” picking systems.
UK online grocer Ocado is one of the pioneers in this area. They have built a number of large automated fulfillment centers to serve larger metropolitan areas. Kroger is partnering with Ocado to build up to 20 automated fulfillment centers in the U.S . Traditional AS/RS and material handling automation providers are getting into the act by developing their own turn-key fulfillment solutions for high throughput, high SKU ecommerce operations.
In contrast to Ocado, which is focusing on large facilities, some other grocery retailers are using similar types of automation technologies to build micro-fulfillment centers in urban or suburban locations. A number of North American Grocers are installing micro-fulfillment centers within or adjacent to existing stores. Loblaw, for example, is building an automated micro-fulfillment center within a large store in Toronto in partnership with Takeoff Technologies.
Outside of grocery retail, few other industries can justify the multi-million-dollar investment costs for these advanced, automated goods-to-person solutions – whether in all-new dedicated ecommerce fulfillment centers, or in existing DCs.
Autonomous mobile robots, or AMRs, are the latest trend in warehouse automation. AMRs use many of the same technologies as self-driving cars and trucks. Scores of start-up robotics companies are applying these technologies in a variety of AMR solutions specifically targeting the warehouse and distribution market. (Still other companies are developing robots that can both pick and transport products, but these systems are early in their commercialization so are not considered here.)
1) Goods-to-Person AMRs
Today’s goods-to-person AMRs take two forms: some that take cartons from shelves to picking stations and others that carry shelves to pickers, similar to Kiva. These solutions are typically paired with dedicated pick-pack stations. They are most applicable to each picking operations with relatively small order sizes.
2) Autonomous Picking Carts
Other AMR systems are intended to function as self-driving picking carts that pickers follow to complete their jobs. The carts may be outfitted with a tablet, scanner and lights to give users their picking instructions and confirm activities. These solutions save users travel time moving carts to and from picking zones, but they do not measurably impact travel within the picking area itself.
3) Conveyance Robots
Several start-up companies are offering robots that are intended to convey products over long travel distances between DC areas. These conveyance robots offer DCs a more flexible and cost-effective alternative to conveyors or traditional AGVs.
4) Autonomous Lift Trucks
There are also a number of companies with a new take on AMRs for full pallet operations. Several start-ups and traditional fork truck manufacturers are adding vision guidance to warehouse vehicles so they can operate autonomously (or, in some cases, semi-autonomously). These self-guided lift trucks show great promise for reducing labor in the most travel-intensive activities in the DC, like pallet put away and replenishment. These tasks, however, don’t typically require as much labor as each or case picking operations.
5) Robots-to-Goods Picking
The latest twist on AMRs for each picking is robot-to-goods AMRs, or swarming robots. In this approach, numerous AMRs travel among workers in pick zones. The robots carry totes to pick locations and meet workers who pick and place the items in the totes based on instructions on a tablet mounted to the deck of the robot. Some ecommerce DCs report doubling or tripling the productivity of their pickers, with a ratio of three or four robots per picker (this is a similar ratio to goods-to-person AMR systems).
The robot-to-goods approach is being used today primarily for each picking in ecommerce fulfillment centers. Unlike goods-to-person AMRs, the robot-to-goods model does not completely eliminate human travel. One drawback is that the pick sequencing is intended to optimize robot activity, not necessarily the travel or activity of the workers. And top potential pick rates for robot-to-goods systems are less than half of the maximum rates for Kiva-style goods-to-person systems.
Compared to traditional fixed automation systems, AMRs offer a number of advantages, including flexibility, scalability, and lower cost.
- Flexibility : Since AMR’s have free reign to travel throughout a facility, they can often be deployed in existing facilities. In addition, DC layouts can be changed after deploying robots without reconfiguring any hard infrastructure. Likewise, you can define new drop off or induction points on the fly through software.
- Scalability: While traditional automation systems are sized to handle maximum throughput (which may only be reached for a few weeks or months per year), robotic solutions can be scaled up or down by adding or subtracting robots and/or pick-pack stations.
- Cost: AMRs cost significantly less than conventional automation systems, but they are by no means a low-cost solution. For DCs that couldn’t justify an investment in conventional automation systems, conveyance AMRs have significant cost and ROI advantages. But goods-to-man or robot-to-goods AMRs offer a less compelling investment case. These AMR picking systems require three or more robots per picker, which represents an initial investment of greater than $1,000,000 for a relatively small operation.
Lucas Systems has taken a different approach to reducing warehouse travel that builds on lean process engineering and applies AI-based optimization technologies that we refer to as Jennifer™ intelligence.
Jennifer increases pick density and reduces travel in picking and other travel-intensive DC activities. Additionally, AI-based optimization does not require any changes to warehouse layouts or storage systems, and the upfront cost is fraction of robotic picking solutions. In addition, Jennifer simultaneously optimizes the travel of robots side by side with people.
Using AI to optimize DC processes has proven to be powerful in ecommerce pick-to-cart operations, where initial customers report doubling productivity without any fundamental changes to their picking processes. Although the biggest productivity gains are seen in each picking, the tool is equally applicable to case picking, replenishment, and other activities where workers are visiting many locations per work assignment.
Jennifer reduces travel through multiple components:
1) Intelligent Batching
Jennifer uses order, inventory, and location information from WMS and other systems and applies real-time optimization algorithms to create batch assignments. Unlike simple rule-based batching used in a WMS (such as FIFO or product and location overlap), Jennifer considers order priority, pick location, travel cost, product attributes, and other factors to create optimal batches of work.
Jennifer evaluates millions of potential combinations to determine the “best batch” or grouping of work from among the available orders. The math behind this is daunting. If 1000 orders are available for batching, and you are trying to create batches of four orders, there are more than 41 million possible combinations. Jennifer runs through the combinations in less than a second as users on the floor request work.
2) Path Optimization
Traditional picking systems use simple pick sequences that direct workers up one aisle and down the next in a snaking pattern. Jennifer’s path optimization algorithms use a virtual map of a facility to compute an ideal travel path that does not follow a strict location sequence. The algorithms take account of a user’s starting and end points, aisle travel restrictions (one-way aisles, for example) and other factors.
Path optimization is applicable to picking, replenishment and other activities where individual work assignments span widely dispersed locations.
3) Waveless Picking/Order Streaming
Jennifer supports waveless order picking (sometimes called “order streaming”) which enables DCs to continuously prioritize, batch and release work as new orders are received. Jennifer makes incoming orders available for picking as they are received. The order pool is continually updated, so that an order received at 2 pm can be released for picking almost immediately. (For more detail on waveless picking, read our recent blog, “Waveless Picking is a Key Capability for E-commerce Fulfillment” )
4) Dynamic Order Prioritization
To increase pick density and create better batches, Jennifer™ prioritizes all available work assignments based on rules that supervisors, in the management console, can configure and adjust throughout the day or week. Rules can be based on ship dates, routes, carriers, order types and more.
5) Robot and Human Work Orchestration
For DCs that have or are implementing AMRs, Jennifer coordinates and optimize the movements of people working with AMRs , driving further improvements in labor productivity and overall efficiency. For example, while within picking zones, a DC can add robots for conveyance between pick zones or other staging locations. This can further reduce worker travel to and from fixed drop off or induction points. Likewise, Jennifer can be used to optimize the travel of robots for full pallet moves, both in inbound and outbound operations.
- Increased productivity and throughput : Based on dozens of trials and successful implementations, AI-based optimization has reduced warehouse travel up to 70%. A number of DCs have more than doubled pick rates in cart pick operations. Baptist Health South Florida saw a 100% increase in picking productivity in their main-piece picking area of the DC. Grocery and food DCs have also seen 15-30 percent savings in travel time in case pick applications , which translates to 8-15% productivity gains.
- Labor savings: Customers utilizing AI-based optimization have also seen major reductions in labor hours. For example, Apex Tool Group, a leading manufacturer of hand and power tools, now operates with 10% fewer person-hours . The most we’ve seen is a 50% reduction in labor hours.
- Increased throughput and shorter turnaround times : Improved productivity and a steady work release (through waveless picking) increases throughput and results in more efficient allocation of workers and equipment. Next-day and two-day orders are out the door on time and in the hands of the consumers on promised delivery dates. For example, Rotary Corp, the worlds largest supplier of power equipment parts, was able to achieve 99.99% same-day shipping.
What Strategy Is Best For My Warehouse?
To choose the best travel reduction/productivity strategy, warehouses and distribution centers need to look at their budget, current processes (case picking vs piece picking), facility size/SKU count, current infrastructure, etc.
However, we’ve learned that many top-performing DCs have maxed out their productivity gains and travel savings through traditional travel reduction strategies. For example, slotting solutions are stagnant and happen once. Without implementing solutions that utilize AI and machine learning algorithms to sot dynamically, most DCs won’t see impressive and continuous results in an ever-changing market.
Given these changing market factors, most facilities are looking for other ways to eliminate travel that don’t require fixed, inflexible automation systems. Robotic systems offer a more cost-effective, flexible, and scalable alternative to traditional material handling systems.
For DCs looking for a low-risk, high-return solution that can be implemented quickly AI-based optimization may be the answer. Lucas AI-based optimization has more than doubled productivity without requiring any changes to warehouse layouts or storage systems. In addition, the technology can be used to optimize the work of people alongside robots, allowing DCs to add more AMRS where they make the most sense today.
Share This Story, Choose Your Platform!
Join our newsletter.
" * " indicates required fields
Continue Reading
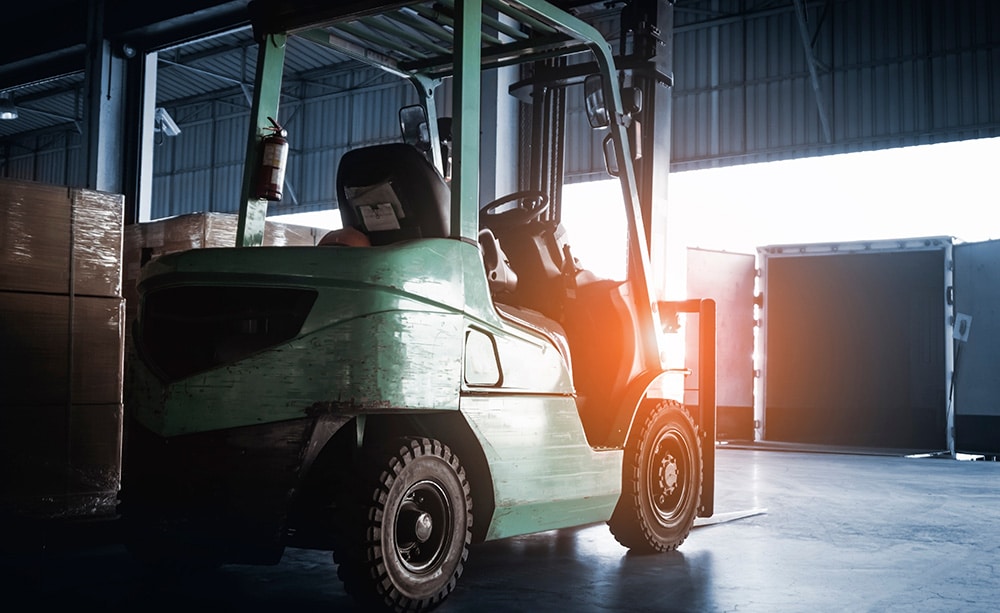
Four Ways Task Interleaving Can Improve Warehouse Processes

A guide for bringing cloud-based software to your warehouse

Which Mobile Applications Are Right for Your Warehouse Operations?
Ready to create an agile, optimized dc operation.
Let’s turn your distribution operation into a competitive advantage, together.
For the past 25+ years, Lucas Systems has helped hundreds of companies transform their distribution center operations using AI, smart software, and voice.

Business Info
Lucas Systems, Inc. 150 North Meadows Drive Wexford, PA 15090
Lucas Systems Ltd. (Europe) Greenwood House London Road Bracknell RG12 2AA
© 2024 • Lucas Systems

The next evolution of warehouse workforce engagement
No thanks, I'm not interested!
Driving Sustainability by Minimizing Distances Traveled in the Warehouse

Photo: Bloomberg
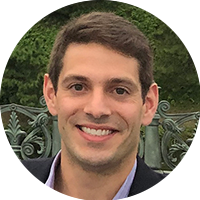
Reducing Forklift Travel Inside a Building
By implementing sustainable practices in scheduling all work, warehouse operations can reduce their environmental impact and save money. One aspect of this is optimizing forklift travel distances within the warehouse. The average liquid propane forklift consumes about 1.5 gallons of fuel per hour, generating around 19 pounds of CO 2 during that period. At a speed of 10 miles per hour, a forklift adds 1.9 pounds of CO 2 to the environment for every mile traveled. Reducing the distance traveled inside the warehouse can significantly lower these emissions.
To minimize forklift travel distances, warehouses can implement the following strategies:
- Efficient warehouse layout: Designing a warehouse layout that minimizes travel distances between storage areas, loading docks and other key locations can significantly reduce forklift travel distances. This may involve placing high-demand items closer to loading docks or using data-driven techniques to optimize the arrangement of storage areas.
- Improved door assignment: Assigning the best door for all inbound and outbound shipments can reduce the need for forklifts to travel long distances within the warehouse by minimizing the total travel distance per pick or putaway. This reduces the time spent on each item, which in turn reduces transportation-related emissions.
- Adopting directed work in the warehouse management system (WMS): Directed work within the WMS can help optimize forklift routes by creating a pool of work considering real-time data on inventory locations, warehouse layout and other factors, and then assigning that work to the closest person. This reduces “deadhead” travel distances, or unproductive travel. Even saving two seconds of deadhead travel per pick can save hundreds or thousands of miles over the course of a few weeks.
- Using automated guided vehicles (AGVs): AGVs can help reduce forklift travel distances by automating the movement of goods within the warehouse. These vehicles follow predetermined routes, minimizing the distance traveled and improving overall warehouse efficiency.
Other Easy Wins
Another warehouse waste that can harm the environment is poor warehouse positioning. Not having the warehouse at the right location means excess movement of trucks between the warehouse, production, distribution center, or manufacturing location. Correctly positioning a warehouse in the supply chain network can help the environment in several ways.
- Reducing transportation distances: By positioning a warehouse closer to suppliers, manufacturers, or end customers, the transportation distances for goods can be reduced. This can lead to a decrease in fuel consumption and greenhouse gas emissions.
- Optimizing transportation routes: A strategically placed warehouse can help optimize transportation routes, reducing the number of trucks on the road and minimizing the carbon footprint associated with transportation.
- Reducing waste: Proper positioning of a warehouse can also help to reduce waste. For example, if a warehouse is located closer to suppliers, it may be possible to order smaller quantities of inventory more frequently, which can help reduce the amount of unsold or expired inventory.
- Improving energy efficiency: By selecting a location that is designed for energy efficiency and incorporates sustainable materials, it is possible to reduce the environmental impact of the warehouse itself; for example, choosing a warehouse powered by solar panels or wind energy.
Connecting Production to Distribution Helps the Environment
It's pretty standard that the movement of products directly from production to various deployment destinations is challenging, due to the complex interplay of production, warehousing and transportation. Often, there is a mismatch between pre-built stock transfer orders (STOs) and what gets produced. Without the buffer of the warehouse storage, line-to-truck struggles to have a ready supply of trailers that match production. Trailers may have to wait idling in the warehouse yard until inventory is available to load the truck. Truck idling means carbon emissions and air pollution.
Technology exists that moves production runs directly to the truck, eliminating touches, reducing the need for storage space at the manufacturing site, and reducing truck idling while waiting for a product to be available for loading. This technology creates transportation requirements days in advance so that best-cost carriers can be engaged. As production changes, transportation can be rescheduled to match production schedules. Each hour, the need and timing of trailers and inventory are updated so everything is synchronized. The right amount of inventory is at the loading dock at the right time with the right amount of labor so that products are loaded quickly, and idling is reduced.
Reducing the distance between products and transportation speeds fulfillment, which in turn helps with sustainability efforts by having the correct number of trucks arrive at the location at the right time. Manufacturers can free up upwards of 10% of space capacity by moving products from production directly to the truck. Less warehouse space needed equals less energy used.
RELATED CONTENT
RELATED VIDEOS
Related Directories
Tecsys, inc., how to improve order fulfillment with ai, subscribe to our daily newsletter.
Timely, incisive articles delivered directly to your inbox.
Popular Stories
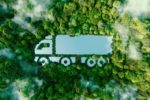
Sustainable Supply Chains: Automating for Transparency and Compliance
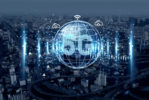
5G Is Here — And With It, Greater Vulnerability to Cyberattack
-in-Newark-New-Jersey.-Photographer-Bing-Guan-Bloomberg.jpg?height=100&t=1711426239&width=150)
United Air Calls Off May Investor Day After Safety Incidents
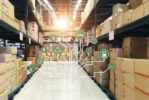
Charting a Sustainable Path: Retail Supply Chain Evolution in 2024
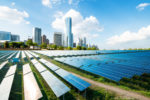
U.S. Treasury Secretary Mulls Possible Tariffs on Green Energy Exports from China
Digital edition.
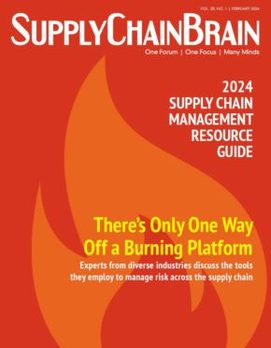
2024 Supply Chain Management Resource Guide: There's Only One Way Off a Burning Platform
Case studies, recycled tagging fasteners: small changes make a big impact.

Enhancing High-Value Electronics Shipment Security with Tive's Real-Time Tracking

Moving Robots Site-to-Site
Jll finds perfect warehouse location, leading to $15m grant for startup, robots speed fulfillment to help apparel company scale for growth.
- Company News
Consulting Services
- Fire Protection, Life Safety, and Accessibility Code Consulting
- Healthcare Specialty Consulting
- NFPA 241, Construction Fire Safety, Permitting and Turnover Consulting
- Laboratory / Industrial / Hazardous Chemical Compliance Consulting
- Battery & Energy Storage System Fire Safety
Inspection, Testing & Commissioning
- Fire Door Testing and Inspections
- Firestop Special Inspections
- Life Safety System Re-Commissioning & Retro-Commissioning
- NFPA 3, Fire Protection System Commissioning and NFPA 4 Integrated Fire Protection and Life Safety System Testing
- Smoke Control Special Inspections
System Design
- Fire Alarm System Design
- Performance-Based Design
- Smoke Control System Design
- Fire Protection System Design
- Third Party Reviews

Back to Insights
Measuring Exit Access Travel Distances
October 10, 2022 by Nick Ostrowski
The exit access configuration within a building is impacted by multiple code requirements to ensure that occupants can safely reach an exit and continue to the exit discharge. One of the major limitations that is required to be evaluated when configuring the exit access arrangement is Exit Access Travel Distance. Exit Access Travel Distances are limitations that identify the maximum distance from any point of a story to an exit. These are measured along the exit path from the most remote point of a story along the natural and unobstructed path of horizontal and vertical egress travel to the entrance to an exit (2015 IBC 1017.3). An exit can include exterior exit doors at the level of exit discharge, interior exit stairways and ramps, exit passageways, exterior exit stairs and ramps and horizontal exits.
Although IBC Section 1017.3 and NFPA 101 Section 7.6 outline how this measurement is taken, there are some common questions raised specific to this process given the different components exit access configurations consist of. The following include a few clarifications to address some these misconceptions while measuring Exit Access Travel Distances:
- Travel Distances are measured to the nearest exit , not all exits. The most remote point on the floor is required to be within the exit access travel distance limitations to any one exit on the floor.
- Often, travel distances change throughout the design of a project. Introducing new furniture or wall partitions for a tenant fitout or alternate furniture layout on a floor may obstruct an existing exit access path. As a result, the new exit access path could exceed the maximum travel distance beyond what is permitted. As design changes take place, it should be confirmed that compliant exit access travel distances are maintained.
- If an exit access stairway or ramp is provided along the path of travel, the Exit Access Travel Distance includes the travel down the exit access stairway/ ramp. The measurement along exit access stairways is required to be made on a plane parallel and tangent to the stair tread nosing’s in the center of the stair and landings. The measurement along ramps is required to be made on the walking surface in the center of the ramp and landings.
It is important to understand how to measure exit access travel distances. If you have any questions on or concerns about this information, please contact our office at [email protected] .
Application of any information provided, for any use, is at the reader’s risk and without liability to Code Red Consultants. Code Red Consultants does not warrant the accuracy of any information contained in this blog as applicable codes and standards change over time. The application, enforcement and interpretation of codes and standards may vary between Authorities Having Jurisdiction and for this reason, registered design professionals should be consulted to determine the appropriate application of codes and standards to a specific scope of work.
Related Posts
EGRESS – PART 3 10th Ed. MA Code Changes
Elevator Means of Egress
Horizontal Exits Design Considerations

Stellar Food for Thought

The International Building Code’s Modification to Exit Access Travel Distance
- Strategic planning
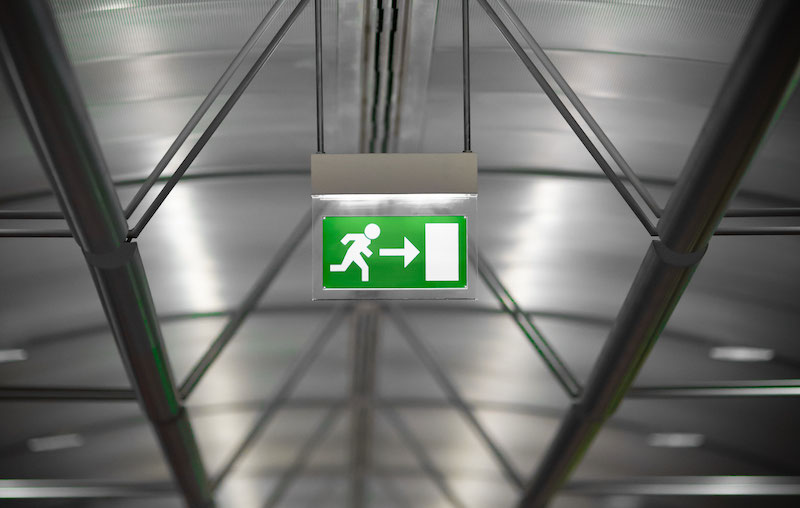
The 2015 International Building Code includes a key modification, increasing the length of exit access travel distance from 250 feet to 400 feet (if it meets specific criteria) for buildings containing Group F-1 and/or S-1 occupancy. This change is significant to the design industry, building owners and occupants of large distribution and manufacturing facilities. Understanding the code’s implications for your existing and future facilities will ensure you’re properly prepared.
A brief timeline of exit access travel distance
1994: In the 1994 Uniform Building Code, the exit access travel distance in a building protected with a fire sprinkler system was typically 200 feet . The exit access travel distance could be increased to 400 feet when facilities storing or manufacturing noncombustible products were provided with smoke/heat vents in addition to the fire sprinkler system.
1997: In the 1997 Uniform Building Code, this section was revised to allow this increase to apply to all warehouses and factories if they were protected with a fire sprinkler system and smoke/heat vents . This exit access travel distance increase resulted in larger buildings with open, undivided areas. A typical warehouse ranged from 600 to 700 feet wide. As buildings continued to grow, 600 feet became the narrow dimension for a warehouse, with many buildings exceeding 1,000 feet in length.
2009/2012: The 2009/2012 editions of the International Building Code were revised to eliminate the 400-foot exit travel distance for large Group S-1 warehouses and large Group F-1 manufacturing facilities equipped with smoke and heat vents. This change was made because thermally activated vents were judged not to warrant such an increase.
The effects of eliminating the 400-foot exit travel distance
Due to the 400-foot loss, designers had to modify new warehouse and manufacturing facilities’ proportions or incur the cost of providing additional exits. And while it was clear to many in the industry that the original rationale for 400 feet was faulty, eliminating the requirement in its entirety was not an option. The industry focused on ways to increase the travel distance for large buildings containing Group F-1 and/or S-1 occupancy.
Task Group 400
An industry group in California came together as “Task Group 400” and conducted a fire modeling study, which demonstrated that the vast volume of large buildings could be used to contain smoke. The group’s report was reviewed by the California State Fire Marshal’s Office and presented to the California Building Standard Commission, requesting a reinstatement of the 400 feet travel distance without any special protection, provided all of the following are met:
1. The portion of the building classified as Group F-1 or S-1 is limited to one story in height 2. The minimum height from the finished floor to the bottom of the ceiling or roof slab or deck is 24 feet 3. The building is equipped throughout with an automatic fire sprinkler system in accordance with Section 903.3.1.1.*
* Reference made to the 2013 California Building Code
The exit access travel distance reversal was successfully passed, and California adopted an amended version of the 2009 International Building Code as the 2010 California Building Code.
California’s code change was later adopted into the 2015 edition of the International Building Code — the model code for most states.
It should be noted that, although code no longer requires smoke and heat vents for this travel distance increase, vents or mechanical smoke removal system, are still required by Section 910.3** and 910.4** for Group S-1 and F-1 buildings of more than 50,000 square feet. There are exceptions, however, for frozen food warehouses and areas with specific types of sprinkler systems.
2 thoughts on “ The International Building Code’s Modification to Exit Access Travel Distance ”
Is “exit access travel distance” just a bureaucrat’s confusing phrase to mean “exit travel distance”? I have a 200 foot wide warehouse, type 2b construction, no interior walls or partitions. Am I correct in using Table 1017.2 for my travel distance “exit access travel distance” for my exit travel distance?
The differences between the terms Exit and Exit Access are defined by the building code in Chapter 2 in the following manner.
“EXIT. That portion of a means of egress system between the exit access and the exit discharge or public way. Exit components include exterior exit doors at the level of exit discharge, interior exit stairways and ramps, exit passageways, exterior exit stairways and ramps and horizontal exits.
EXIT ACCESS. That portion of a means of egress system that leads from any occupied portion of a building or structure to an exit.”
Exit components such as interior exit ramps, interior exit stairs or exit passageways are separated from other interior spaces by fire-resistance-rated construction. If there are no interior exit stairs, passageways or ramps, then your exit access travel distance would be from the most remote point to the nearest exterior exit door if it is at the level of discharge. If the exterior exit door is not at the level of discharge, then the exit access travel distance continues to the level of discharge unless the exterior ramp or stairs is considered an exterior exit stair or exterior exit ramp and is protected from the interior of the building by fire-resistance-rated construction.
You are correct in using Table 1017.2 to determine the travel distance limitations.
Conversation Cancel reply
Your email address will not be published. Required fields are marked *
Save my name, email, and website in this browser for the next time I comment.
Post Comment
Travel Distance Calculation
The travel distance calculation calculates the travel distance that a warehouse worker must travel to execute a warehouse order.
There are two types of network :
● Storage-type-specific networks, which you define for each storage type. These comprise the following:
○ Edges that correspond to the aisles of a storage type
○ Edges that connect these aisles to each other
● Global network that connects the storage-type-specific networks to each other.
You create both of these networks in the Settings for the Travel Distance Calculation . You can also generate storage-type-specific networks using the program Generate Network .
In addition to calculating the travel distance, the system determines the time required by a worker to execute the warehouse order, depending on the speed of the resource used.
Integration
The result of the travel distance calculation is used for:
● Planning the workers, if you have activated Labor Management (LM).
● Calculating engineered labor standards (ELS), if you have activated LM.
● Calculating the latest start time for a warehouse order.
If you want to use the travel distance calculation, you have to configure it. On the SAP Easy Access screen, choose Extended Warehouse Management → Settings → Travel Distance Calculation → Settings for the Travel Distance Calculation.
● Direct distance
The system calculates the travel distance using the direct distance, based either on the Euclidean or Manhattan Metric.
The figure below shows the direct distance between two storage bins of a storage type. The solid line corresponds to the Euclidean metric, the dotted line represents the Manhattan metric.
● Distance based on networks
The travel distance calculation can also be based on an existing valid network. The valid routes represent the edges.
The figure below shows the distance between two storage bins of a storage type. The resource moves across the valid routes.
● The system calculates the travel distance needed to execute a warehouse order more than once, namely when:
○ Creating a warehouse order for planning purposes
○ Confirming a warehouse order for evaluation purposes
Only when confirming is the system able to access more detailed information, as only then is the executing resource known. The following information is then available:
○ Speed of the resource
○ Last position of the resource prior to executing the warehouse order
○ The route network allowed for the resource, if available
When calculating the distance while creating the warehouse order, the system estimates the following values:
○ For the speed, the system uses the speed of the slowest resource (pessimistic approach).
○ Instead of the known position of the resource, a default distance to be covered in order to reach the first position in a storage type is specified.
○ The route network used (if available) contains all defined routes without resource type restrictions.
● The system saves the result of the travel distance calculation in the planned and executed workload, if Labor Management (LM) is activated.

- Search forums
- Welcome to the new and improved Building Code Forum. We appreciate you being here and hope that you are getting the information that you need concerning all codes of the building trades. This is a free forum to the public due to the generosity of the Sawhorses, Corporate Supporters and Supporters who have upgraded their accounts. If you would like to have improved access to the forum please upgrade to Sawhorse by first logging in then clicking here: Upgrades
- Commercial Codes
- Commercial Building Codes
Restroom Travel Distance
- Thread starter fatboy
- Start date Dec 1, 2009

Administrator
- Dec 1, 2009
Ok, we have a new developement where the anchor store is also installing the fueling station, without restrooms. It was identified at plan review that the travel distance for the fueling station kiosk to the store was over 500', that they need to provide restrooms at the liosk, or move it closer, to comply with 2904.2.1. They have provided a drawing that shows the travel distance to be 504', from the door of the kiosk, to a mid-point in a foyer between the men's and womens restroom doors. They consider this to be the travel distance. I have maintained that the "path of travel" was from where one may be in the kiosk, to the most remote fixture in the store that may be need to be used, along a logical path. To the most remote fixture in either restroom it is another 24'. The kiosk interior, probably another 10' to the most remote point, so we're pushing 540'. The applicant is asking me to allow this to happen, based on future platted pad sites that would easily make the 500'. I'm still saying no, but am curious if I'm just being one of those a$$hole officials that is being non-friendly to developement, by not ignoring that silly 500' "shall not exceed" prescriptive requirement. What say ya'll?

Silver Member
Re: Restroom Travel Distance I probably wouldn't get excited over 500' vs. 540' (unless I really had to go!), but more importantly, is the distance measured along a path that actually is available to the user? By that I mean, did the designer measure as the crow flies, or did he allow for vehicles actually parked in the paking lot, etc.? I had a designer show that the fuel kiosk (Sam's Club) was less than 500' , however, he was measuring diagonally across a parking area. When measured according to an actual palth it was over 700' !!! By the way, the "future sites" the designer refers to might not work... The fuel kiosk has to be associated with the store that has the restrooms (same hours, etc.) otherwise closer restrooms (owned by individual tenants) may not be available when the fuel kiosk is open for business.

Platinum Member
Re: Restroom Travel Distance to add to what vp was saying; is there an accessible path providing safe travel to and from the restroom? would not want anyone getting ran over while wheeling or dashing through the snow to the bano~. make em build a complying restroom,your wife will appreciate it!

Forum Coordinator
Re: Restroom Travel Distance Could you defend your decision in court? That is your answer.

- Dec 2, 2009
Re: Restroom Travel Distance No Fatboy! Not silly! Tell him to go to the appeals board or put in the bath room. I believe we will see more of these issues as Super Markets and Big Box stores want to have gas as an added use. Have one near me in another ahj doing the same. Can't wait to see it finished. They have not provided bath rooms! Distance to the store is over 600'. I pop the question when they are finished! :lol: The code is what it is!

Gene Boecker
Gold member.
Re: Restroom Travel Distance By anchor store do you mean as in a strip center or as in "covered mall?" The travel for a covered mall is 300 feet. And, as far as measuring is concerned, I've usually seen that done to the door of the restroom although if you go inside the room, I'd use the first WC - not the most remote. Why make them go past a usable fixture? Measuring from the most remote point inside the kiosk makes sense though. Betting on the future pad development is a bit thin, I agree. Why not split the difference and make them park a half dozen porta-potties outside the front door? Give them THAT choice and see what they pick..

Re: Restroom Travel Distance Fatboy, We had one of those done here. They put a restroom into the little station hut, but no open or accessible to public. I think it was 700' to the store itself and another 200 to the bano. I know that whether these pump&pays have public BR has been a topic of discussion as well, but I think practicality demands at least one for the attendant. Usually only one person attends.
- Dec 3, 2009
Re: Restroom Travel Distance Answers to the questions in no apparent order. The first plan they submitted was as the crow flies, which was rejected quickly, the path they show now is sidewalk with curb-cut ramps, so it ias accessible. I'm not buying the other future sites for those reasons, when and if they will build out, hours of operation conflicts..... Anchor store, as in for the developement, it is a stand-alone structure. The reason I feel the path of travel should be to the furthest fixture is that the furthest fixture may be the only one available at any given time. Jeff poses the question I'm have been hung up on from the onset, and no, if I allowed this I wouldn't be able to defend it in court. I'm going to reject their appeal to me, I don't think they would really stand a chance with our BOA, since by their own admission they are over 500' between the points they are measuring. A BOA cannot disregard the code requirement of 500', only rule on interpretations, the only thing I interpreted was what constitutes the "path of travel". Furtunatelly I have my boss behind me. Thanks for the replies!
Re: Restroom Travel Distance fatboy - is the anchor store and the fuel station the same company (e.g. Sam's Club) or are they claiming that the independent gas station can use the anchor store's restrooms just because of proximity? I would DEFINITELY deny it if it were two different companies.
Re: Restroom Travel Distance No, same company will own both the store and fueling station, but not the suggested future pad sites.

Registered User
- Dec 10, 2009
Re: Restroom Travel Distance fb - At least you're getting support from above. Not all of us are that lucky...
Re: Restroom Travel Distance So now I'm trying to figure out how the self-fuleing Costco station can have an attendant's cabin but no restrooms. . . . .
Re: Restroom Travel Distance I was on the phone with the applicant again this morning, who was still asking for lenience on my interpretation. Said they had built them all over CO with nobody ever enforcing this requirement. He did finally ask about a porti-potty till the pad sites were built out. Told him the the porti didn't meet the code requirements for a restroom. Stuck with my original call, move it or install compliant restroom. Yes, I am lucky that I have the support from above.

Mr. Inspector
Re: Restroom Travel Distance I had one of these. Made them put in a accessible restroom in the attenant's building. Went to get gas there two days after the c/o was issued, the rest room sign was gone, the door was locked, and the attenant said there is no restrooms.
Re: Restroom Travel Distance Oh well, it was there when the C.O. was issued, you did your job.
Re: Restroom Travel Distance Rick - You'll have to bang them for the violation at their (annual?) Fire Safety Inspection.
\ said: . I'm going to reject their appeal to me, I don't think they would really stand a chance with our BOA, since by their own admission they are over 500' between the points they are measuring. A BOA cannot disregard the code requirement of 500', only rule on interpretations, the only thing I interpreted was what constitutes the "path of travel". fatboy, would you allow an increase in travel distance if they sprinkled it? :mrgreen: Click to expand...
Re: Restroom Travel Distance Because water cascading down on you while you rush to the bathroom will somehow make the trip more bearable? :lol:
Re: Restroom Travel Distance pwood, you're absolutely right about your position. An appeal means that you both may not be interpreting the provision in the same way and you need a referee. What they are asking for is a variance. That's a whole separate issue although they often act the same. jd, where is that water running down???? :lol:
- Dec 11, 2009
- Dec 18, 2009
jar546 said: Could you defend your decision in court?That is your answer. Click to expand...

IMAGES
COMMENTS
This exit access travel distance increase resulted in larger buildings with open, undivided areas. A typical warehouse ranged from 600 to 700 ft wide. As buildings continued to grow, 600 ft became the narrow dimension for a warehouse, with many buildings exceeding 1000 ft in length.
45M in normal fire-risk area. 60m in lower fire-risk area. Where only a single escape route is provided: 12m in higher fire-risk area. 18m in normal fire-risk area. 25m in lower fire-risk area. The travel distances given above are based on those recommended in Approved Document B of the Building Regulation and are intended to complement the ...
The length of common path of egress travel distance in a Group S-2 open parking garage shall be not more than 100 feet. g. For the travel distance limitations in Groups R-3 and R-4 equipped throughout with an automatic sprinkler system in accordance with Section 903.3.1.3, see Section 1006.2.2.6.
Putaway in warehouse processes means storing products inside the warehouse and stacking them on shelves, containers, bins, pallets, and other assigned places. The putaway process starts with placing a purchase order to the vendor. After the vendor sends the products listed in the order, they need to be stored efficiently inside the warehouse to ...
Zone Travel Method. For many facilities, the Zone Travel method is the right balance between accuracy and simplicity. In this approach, a facility is divided into 20-150 "zones" and then the average distance between each zone is calculated. Locations are then assigned to their appropriate zones using the Location Naming Conventions.
Reducing traveling time is another important factor when optimizing the putaway process and warehouse operations in general. The goal is to reduce the time goods travel from the receiving area to the storage location. Travel distance in a warehouse is 60% to 70% of labor cost. To accomplish this, warehouse managers can conduct an ABC analysis ...
Uday Venkatadri and Sachin Kubasad. Department of Industrial Engineering. Dalhousie University. Halifax, Nova Scotia, B3J 2X4, Canada. ABSTRACT. This paper looks at the problem of estimating travel distances for rectangular warehouse sections with manual picking. This study was motivated by a real-life case in the food and beverage industry ...
For the typical Class 7b warehouse building, the following requirements are applicable for egress travel distances under NCC 2019 Amendment 1. Up to 20 metres travel to an exit or a point where travel to a choice of two different exits is possible within a total of 40 metres travel.
The Ultimate Guide To Reducing Warehouse Travel. In Warehouse Travel Optimization. June 30, 2021. Labor is the single largest operating cost in most DCs, and travel often accounts for half of all labor time, especially in order picking. In some DCs, pickers can travel upwards of 12 miles per shift. To help address the warehouse travel challenge ...
By implementing sustainable practices in scheduling all work, warehouse operations can reduce their environmental impact and save money. One aspect of this is optimizing forklift travel distances within the warehouse. The average liquid propane forklift consumes about 1.5 gallons of fuel per hour, generating around 19 pounds of CO 2 during that ...
Means of egress design must consider the distance occupants travel to an exit, how far apart exits are located from one another, and more.
The length of common path of egress travel distance in a Group S-2 open parking garage shall be not more than 100 feet. g. For the travel distance limitations in Groups R-3 and R-4 equipped throughout with an automatic sprinkler system in accordance with Section 903.3.1.3, see Section 1006.2.2.6.
Exit Access Travel Distances are limitations that identify the maximum distance from any point of a story to an exit. These are measured along the exit path from the most remote point of a story along the natural and unobstructed path of horizontal and vertical egress travel to the entrance to an exit (2015 IBC 1017.3). An exit can include ...
This exit access travel distance increase resulted in larger buildings with open, undivided areas. A typical warehouse ranged from 600 to 700 feet wide. As buildings continued to grow, 600 feet became the narrow dimension for a warehouse, with many buildings exceeding 1,000 feet in length.
1030.7Travel distance. The exit access travel distance shall comply with Section 1017. Where aisles are provided for seating, the distance shall be measured along the aisles and aisle accessways without travel over or on the seats. Exceptions: 1. In facilities with smoke-protected assembly seating, the total exit access travel distance shall be ...
When each of these tasks are performed independently, the travel distance increases. In the above 2 scenarios, the distance when forks are empty is equal to 66% of total travel distance.
Purpose. The travel distance calculation calculates the travel distance that a warehouse worker must travel to execute a warehouse order. There are two types of network: Storage-type-specific networks, which you define for each storage type. These comprise the following: Edges that correspond to the aisles of a storage type.
The distance of travel from any point in a smoke compartment to a smoke barrier door shall be not greater than 200 feet (60 960 mm) ... Illinois Building Code 2018 > 4 Special Detailed Requirements Based on Occupancy and Use > 407 Group I-2 > 407.5 Smoke Barriers > 407.5.2 Exit Access Travel Distance
It was identified at plan review that the travel distance for the fueling station kiosk to the store was over 500', that they need to provide restrooms at the liosk, or move it closer, to comply with 2904.2.1. They have provided a drawing that shows the travel distance to be 504', from the door of the kiosk, to a mid-point in a foyer between ...
Find the travel option that best suits you. The cheapest way to get from Moscow to Elektrostal costs only RUB 119, and the quickest way takes just 50 mins. Find the travel option that best suits you. ... The distance between Moscow and Elektrostal is 52 km. The road distance is 48.9 km. Get driving directions
Select an option below to see step-by-step directions and to compare ticket prices and travel times in Rome2rio's travel planner. Recommended option. Train. Take the train from Nizhegorodskaya to Fryazevo. 2h 29m. RUB 481 - RUB 601. 3 alternative options. Train via Kurskaya.
Find the travel option that best suits you. The cheapest way to get from Elektrostal to Moscow costs only RUB 120, and the quickest way takes just 39 mins. Find the travel option that best suits you. ... The distance between Elektrostal and Moscow is 52 km. The road distance is 58.6 km. Get driving directions
Find the travel option that best suits you. The cheapest way to get from Lyon to Elektrostal costs only RUB 20580, and the quickest way takes just 13½ hours. Find the travel option that best suits you. ... The distance between Lyon and Elektrostal is 2580 km. The road distance is 3077.4 km. Get driving directions